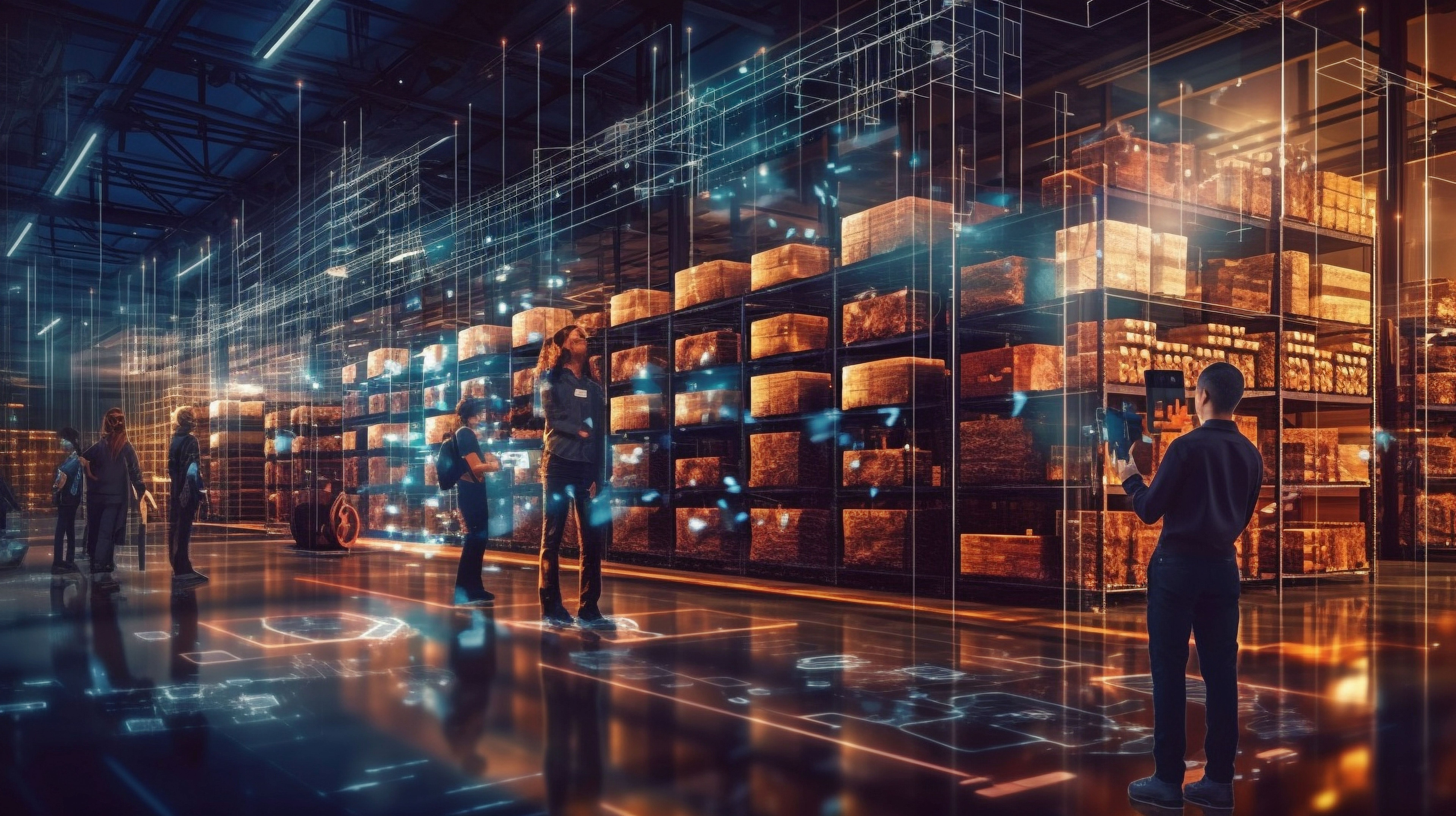
By Jens Bohnwagner, CEO, XSQUARE Technologies
Behind the scenes of any organisation, employees are the cornerstone of its success. In response to this, companies and governments now place greater emphasis on workplace safety and the holistic well-being of employees.
According to a report by the Ministry of Manpower in Singapore, 25,566 cases of work injury claims were compensated in 2022, and the total compensation payout amounted to SGD $122.26 million. This underscores the potential repercussions for companies that neglect workplace safety, including increased financial costs, loss of productivity, reputational damage, and lowered employee morale.
Since most individuals spend a significant part of their lives at work, it becomes imperative for employers to prioritize the health, safety, and well-being of their employees. The equation is simple – well-supported and appreciated employees become engaged and productive, thereby contributing positively to the company and the economy.
The key to business sustainability: Balancing efficiency and safety for employee retention
Amidst the backdrop of labour shortages, the pursuit of business sustainability hinges on retaining employees. Companies are no longer solely focused on profits but are committed to nurturing work environments where employees are safe, supported, and motivated to excel. The key to achieving this balance lies in the strategic integration of automation, especially in sectors like warehouse management.
Automation offers an avenue to enhance workplace safety and well-being by automating dangerous and repetitive tasks, which not only reduces the risks of preventable workplace injuries but also grants employees respite from labour-intensive responsibilities.
This opens doors for businesses to create safer, more conducive working conditions, stimulate a culture of growth and innovation, and invest in the safety and well-being of employees. In doing so, employees have the chance to acquire new skills, leading to heightened job satisfaction and productivity. Ultimately, this creates a high-performance employee environment that fosters healthy business growth and profitability with reduced turnovers and fewer safety incidents.
The human element in automation: Developing a modern workforce
As we transition into the future of automated warehouses, companies are seeing the benefits of upskilling their workforce and promoting collaboration between workers and automated systems, such as robots. This collaborative approach enhances business flexibility, by enabling easy configuration to support demand and production fluctuations.
With automation handling potentially dangerous and tedious tasks, employees can be upskilled to work alongside to operate and maintain these new systems, creating career advancement opportunities. For instance, embracing cutting-edge technology in warehouses, including AI, data analytics, warehouse design, and inventory management, brings forth new roles, such as data analysts, technicians, and engineers, accommodating employees of varying educational backgrounds. A Deloitte report highlights that the creation of highly skilled, better-paid roles through automation enables employees to expand their responsibilities and functions, leading to a heightened sense of purpose and boosting self-esteem and confidence.
The path forward: Achieving a seamless automation journey for warehouse operators
Selecting the right technology is critical to align with your warehouse’s unique needs, placing emphasis on interoperability for seamless integration. This consideration serves as the decisive factor in preventing issues with compatibility or the necessity for costly system overhauls.
Involving employees from the beginning of the transition process fosters collaboration, ensuring a smooth transition and allowing employees to witness the potential benefits and workflow improvements that automation can bring.
Based on a sentiment analysis by Harvard Business Review, employees express concerns about inadequate training to work safely and fix issues with automated tools. To address this, training programs should include hands-on practice and machine operation simulations that include troubleshooting. Businesses must also evaluate safety measures and deploy risk management strategies to ensure compliance with safety regulations. This minimizes safety-related incidents and enhances employees' job satisfaction.
That said, the shift to automation comes with its own set of challenges including the complexity of the implementation process, high upfront costs, intricate software integration, and the time it takes for businesses to reap the ROIs. For example, the implementation process can be resource-intensive, which impacts operational budgets. As such, businesses with resource constraints might consider a more prudent approach to automation, such as adopting a modular strategy for long-term automation plans, with the flexibility to scale up and integrate more automated systems over time.
Final thoughts: Harnessing the potential of employee-centric automation
In the journey toward harnessing the potential of employee-centric automation, we find a powerful convergence of technology and human ingenuity. This synergy not only reshapes the way we work but also redefines the essence of our workplaces. Employees stand as a bedrock of success, not only as beneficiaries but as active contributors in this transformative journey.
Their safety, support, and motivation are the guiding principles, ensuring that automation transcends technological advancement to become a cultural shift that elevates our organisations to new horizons.
Supercharge Your Warehouse Today
Discover how intelligent automation solutions can revolutionise your business operations